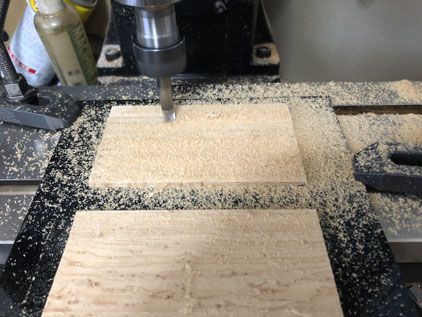
ハンドクラフト展でよく目にするのがWood製FlyBoxです。
高価な銘木で加工されたFlyBoxには憧れがあります。
しかし、高価なので、欲しいけど手が出ないのが本音です。
何故高価なの?
これを解明すればどうすれば安価なFlyBoxが作れるのか判るはずです。
①高級木材で加工している。
瘤材等の高価な材料で加工しているので、そもそも材料費が高価
②厚みのある板材をくり抜き加工している。
大きく、厚みのある材料は高価であり、それをくり抜いて加工しているために材料費が高価になる。
③高価なヒンジを使用している。
ヒンジ(蝶番)はピンキリで、安価なヒンジは安っぽく見え、複雑に開口するヒンジは1個当たり400円以上するので
FlyBoxを作製するのに800円以上のヒンジ代は馬鹿にできない材料コストである。
総合すると、材料そのものの価格が比較的安価な材料を選定し、厚みのある板材をくり抜き加工するのではなく、薄板を貼り合せて加工し、ヒンジ部分の材料コストを抑える工夫をする。
これが安価にFlyBoxを作製ために必要だと判りました。
私は以前より、リールのフェイスプレートやVictorinox等々のカバー材加工用に4mm厚の板材を購入していました。
今回はその板材を使用してFlyBoxを加工してみることにしました。
まず板材を均一な厚さになるよう加工するのですが、プレーナーなどがあろうはずもなく、フライス盤でエンドミル加工で厚さを3.5mmに揃えました。
問題はヒンジ部分です。
ヒンジを購入するからコストアップになるので、ヒンジも作製できないかと考えました。
3.5mmの板材で加工できればコストダウンできると考え、板材でのヒンジの構成を結構考えました。
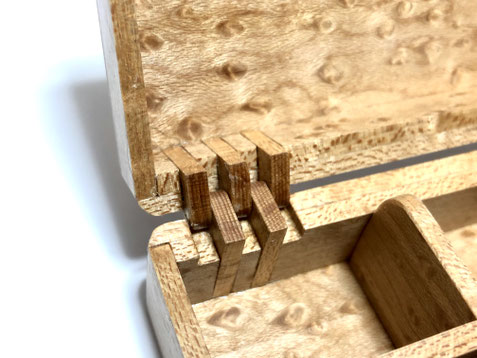
考えた形状がこれです。アルファベットのP形状をした厚み3.5mmの板材を互い違いに配置してヒンジにするという発想です。
このP型ヒンジをいかに精度よく組立て、センス良く見せるかが課題と考え、P型ヒンジが上手く収まる座グリ部分を設けて加工精度の高さを見せつけつつヒンジ部分を敢えてこのFlyBoxの特徴として主張させるようにデザインしました。
このP型ヒンジが収まる部分の部材は3.5mmの板材を2枚重ねて7mm厚にしています。それ以外の部分は3.5mmの板材をそのまま加工して使用しています。
7mm板材と3.5mm板材の接合部分もうまく組み合うように相欠き継ぎを採用しています。
この部分は組み継ぎを採用しても面白いと考えています
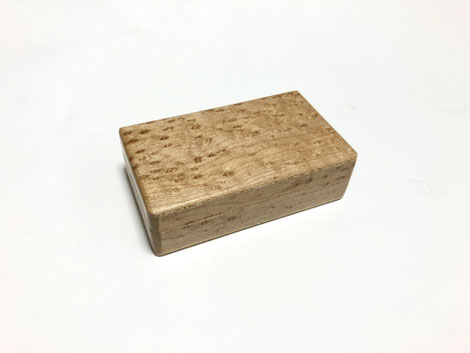
全体像はこんな感じでまず初号機は奇抜なデザインにはせず、シンプルなお弁当型にしています。
板材はバーズアイメイプルで加工しております。
もっと安価な材料でもよかったのですが、我が家にある材料で最も安価な材料がこれだったのです。
3.5mmの板材を切って、貼ってで加工した割にはよくできたのではないかと考えています。
Boxを開ける部分に凹み加工などは施していませんが、今後必要に応じて加工したいと思います。
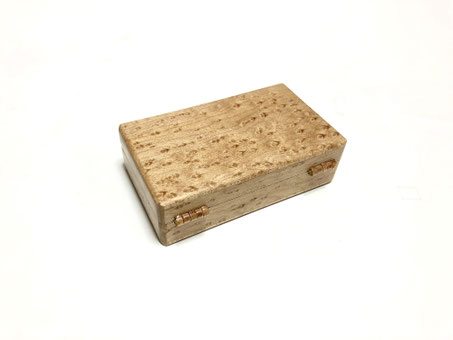
裏側から見た写真がこれです。
P型ヒンジ部分がプクッと飛び出した形状ですが、これがデザイン意匠となります。
金属製のヒンジは出来ることなら隠したいと思うのですが、Wood製のP型ヒンジにすることで見せるヒンジになったと思います。
裏側だけを見ただけではどんなヒンジ構成になっているのか判らないのもいい感じです。
サイズは110mm×65mmで高さ32mmです。
このサイズならベストのポケットに入れても嵩張らないです。
ちなみに重量は39.5gで気にならない重さになっています。
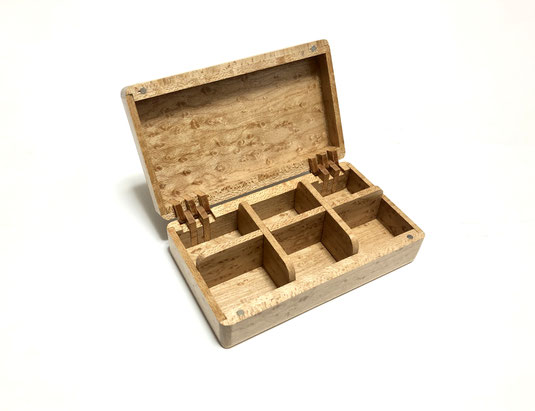
蓋を開けた状態はこんな感じです。
仕切り板も3.5mmの板材で加工しています。
材料としては、3.5mmの板材115mm×65mmを6枚準備します
天板と底板で2枚
ヒンジ部分とマグネット部分には2枚貼り合せて加工しているので2枚
サイド部分に1枚
仕切り板加工に1枚 計6枚で加工しています。
サイド部分の加工した余り材料でP型ヒンジを加工しています。
やはりこのFlyBoxを開けた時にはヒンジ部分に目が行きます。
金属製では隠したい部分であったヒンジをWood製にして、隠さずに主張させることでFlyBoxのデザインの要になっているような気がします。
コーティングはFlyBoxを研磨した後にウレタン樹脂で拭き塗りをしています。
これも漆の拭き塗りにも挑戦したいと考えています。
では、このFlyBoxが安価で作製できたのか?
結論は、材料費は削減出来ました。
加工は複雑なので、掘り込み方式のFlyBoxの方が加工時間は短いと思います。
と言うことで、少しは安くできると思います。
加工条件の更なる見直しで加工時間の短縮を行うのが今後の課題となりそうです。
今回P型ヒンジができましたので、このヒンジを流用するとこで様々な形状のFlyBoxへの展開が「可能になります。