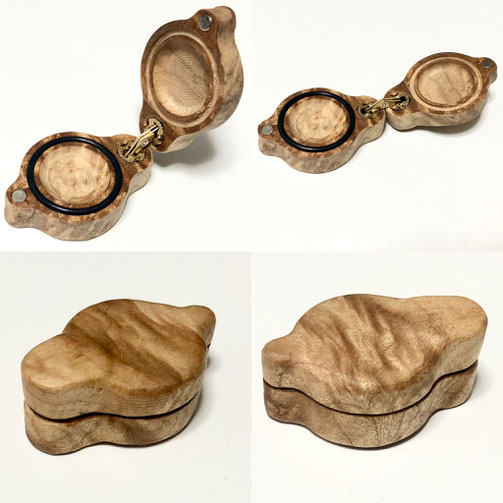
以前も一度ブログで紹介したフロータントケースです。
自転車用のフッ素グリースをフロータントとして使用すると言ったものなのですが、購入したままの容器と言うのがねじ込み式のケースで、実際に渓流で使用した場合、蓋の落下等の恐れがあるのと、いちいち蓋を回す動作がめんどくさいという理由でフロータントケースを作りました。
この時に注意したこととしては、
1)簡単に開閉できること。
2)中身がこぼれ出てこない事
3)水に浮くこと
以上の3点を考慮して設計加工を行ないました。
簡単な開閉のために、キャビネットヒンジを採用しました。
キャビテネットヒンジは8mm径のものを使用しているのですが、このキャビネットヒンジ部分をフロータントケースに埋め込むためにはφ8mmで深さ9mmの円筒状の穴加工が必要です。
ですので、フロータントケースのヒンジ部分の厚みとしては最低でも10mm以上の厚みが必要になってしまうのでした。
フロータントが収まる部分は問題ないとしても、蓋側も10mmの厚みとなるとフロータントケースの総厚20mmとなってしまい、カッコ悪いのです。
仕方なく、蓋側のヒンジ部分以外を少し削って全体のボリュームを少し減らしたようなデザインにしましたが、
自分の思ったようなデザインとは少しかけ離れた形状になってしまったのは事実です。
もう一つ気になったことがあります。
それはキャビネットヒンジそのものなのです。
Fly Boxに使用した際には気にならなかったのですが、キャビネットヒンジを1個使った場合、結構キャビネットヒンジがグラつくんです。
Fly Boxのようにキャビネットヒンジを2個使用する場合はグラつきを吸収することができるんですが、1個使用のままだとグラつきはそのまま蓋部分のグラつきになってしまうのです。
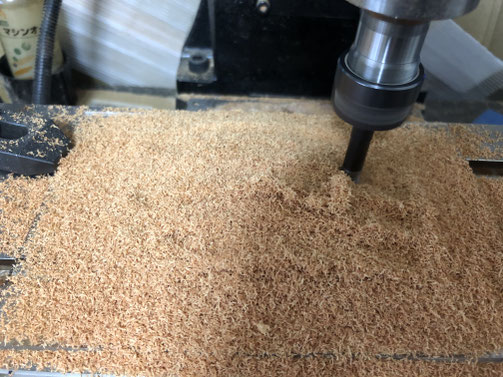
キャビネットヒンジがグラつくのなら、以前から加工しているP型ヒンジやD型ヒンジを使用すれば良いということで、D型ヒンジを使用したフロータントケースを作ってみることにしました。
手持ち材料も良さげなものがなかったので、花梨瘤材の板をフライス加工して厚み調整を行いました。
D型ヒンジを使用することで、フロータントケースの厚みの制約はなくなりましたので、フロータントが収まる部分の厚みを7mmとして、蓋部分を5.5mmの厚みにしようと考えました。
この厚み調整のためのフライス加工が中々めんどくさいのです。
8mmのエンドミルで加工していくんですが、厚み調整する場合の板面積はそこそこ大きいので全面を加工するためには結構な回数をトレースする必要があります。
更には、1回の除去深さは0.4mm程度なので、数mmの厚さを除去するためには繰り返し回数も結構な回数になり、時間が掛かってしまいます。
厚さを調整するためのプレーナーが欲しいんですが、結構なお値段なので....。
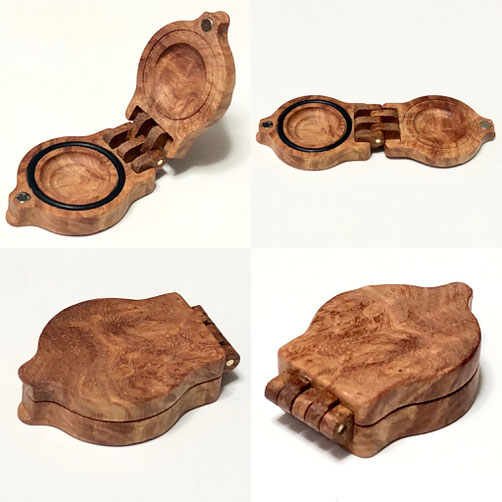
さて、D型ヒンジの場合、フロータント収納側は3つ、蓋側は2とのD型ヒンジを使用することにしました。
構成パーツとしては、7つ加工部品で構成しているので、その分加工時間が長くなるんですが、やはりD型ヒンジを使用したフロータントケースの方が手作り感がでて、雰囲気としては良いと思います。
フロータントの漏れ出し防止にはOリングを嵌め込んでいます。
内径23mm、外形27mmのOリングを使用しました。
Oリングを介してφ4mmのマグネット吸着でOリングを僅かに変形させることで、フロータントの漏れ出しを防止する構成としております。
これに関しては、夏場の灼熱状態でフロータントの状態を確認する必要がありますので、今シーズン使用して様子を見てみようと思っています。
おおよそのデザインはこんな感じなのですが、D型ヒンジの出っ張りをもう少し抑えたような形状にしようと考えております。
今回は花梨の瘤材で加工しましたが、花梨瘤材だと結構な値段になりそうなので、材料についてはもう少し考え直すかもしれません。
あと、今回加工して気づいたんですが、このフロータントケースを使用する場面をイメージした場合、やはり現場での脱落防止のために何かしらの対策が必要です。
穴開けて紐を通すだけでもいいと思うのですが、後一工夫してデビューさせたいと考えております。