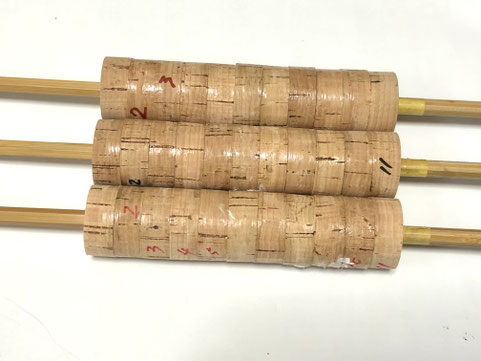
グリップの接着は、まずリールシートフィラーを装着してみて、コルクの最後端位置を確認します。
そして、そのコルクの最後端の1個をエポキシ接着剤で接着し、このコルクを基準にして他のコルクを接着していきます。
今回は11個にコルクを接着いたしました。
コルクの選定としては、旋盤にチャックして回転させ、コルクの変形状態を確認し、振れがあるコルクを除去します。
(振れのあるコルクはまとめて振れが無くなるように端面加工して修正します)
コルクの接着は木工用ボンドで接着を行っています。
コルク接着時は木工用ボンドを手で塗りつけて、コルク同士が密着するときにコルクを回転させて余剰接着剤を排出させます。こうすると傾いた状態で接着させることを防止できます。
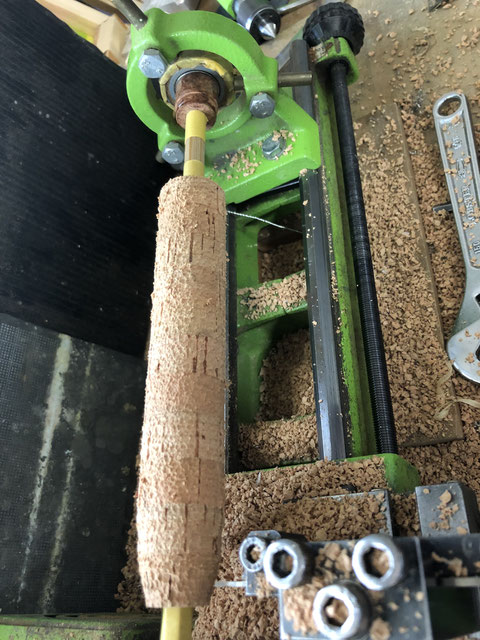
コルクの成形は旋盤を使用し、コルク先端側を主軸にチャックします。
チャック部分にはマスキングテープを巻いて、主軸のチャックによりブランクに傷がつかないようにしています。
リールシートフィラー部分を振れ止めに固定して加工します。
この振れ止めは3本の真鍮棒をネジ固定してセンターを出す治具なんですが、この3本の真鍮棒でφ15mm程度のベアリングを固定し、このベアリングの内径に合わせた外径と、リールシートフィラーと同径のウッドパーツを加工してコルク後端側を保持しています。
コルクの加工は案外負荷がかかるので、突っ切りバイトで加工を行なっています。
切削加工と言うよりはコルクをむしり取ってる感じなので、最終外径よりも2~3mm程度大き目で加工を終了して、残りはサンドペーパーで加工をお勧めいたします。
勿論、掃除機を回しながら加工していきます。
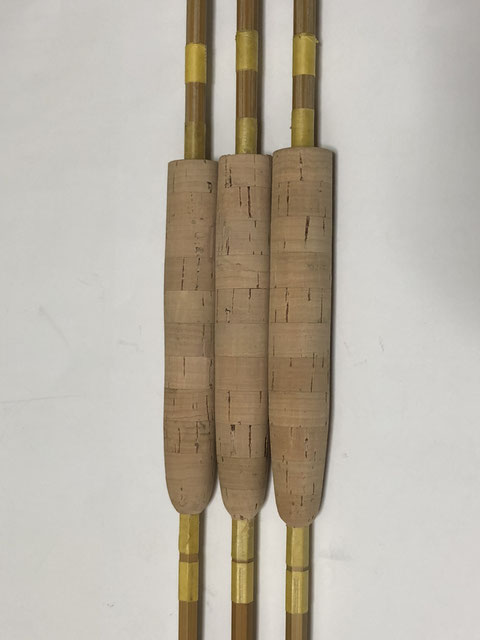
グリップの形状はシガータイプのオーソドックスな形状にしています。
昔はファインシガータイプにしていたんですが、形状的にはカッコいいんですが、実際にキャスティングするにはシガータイプの方が握りやすいので、最近はシガータイプにしています。
もちろんこれは低番手ロッドだからです。
グリップ長さも以前はコルク10個程度でしたが最近は11個にしてゆったり握れるようにしています。
3本同時加工では、コルク接着や、グリップ成形も順次加工となり、効率は良くないんですが、アクション比較しながら加工していくのは楽しくもあります。
さて、この先はラッピング作業となり、同時加工は大変になりますが、もう少しで完成なので、慌てずに丁寧にラッピングしていこうと思います。