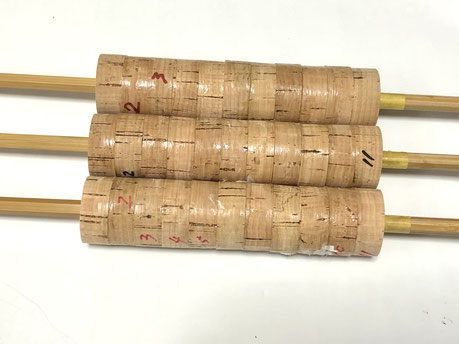
ロッドには欠かせないコルクですが、最近のコルク価格の上昇は凄いですね。
私は知り合いから購入しているのですが、以前よりも値上がりしてるのと、品質が気になっています。
それでも、他のビルダーさんよりも良いコルクを使えていると思っています。
さて、コルクの品質としてはスのお入り具合でグレード分けされていますが、そのグレードも結構いい加減で、結局は採集されたコルクを選別してグレードを決めているとは思うのですが、メーカーというか採集場所と言うか、選別者の感覚的なものが大きいような気がしており、輸入業者ごとに同じグレードでも品質にかなりのばらつきがあるように感じます。
コルクが高値で売れるので、いい加減な選別、高価な値段設定でも売れるので、どんどん品質が低下していってるような気がしてなりません。
これはビルダー側は何ともできないので、信頼できるところから購入するしか手はなさそうです。
コルクのグレードはスの状態で決まりますが、それ以外でもビルダー側からすると使いにくいコルクがあります。
それは、円筒部分と平面部分との直角度です。
コルクはセンター穴の開いたコルクをブランクに押し込んで接着していき、硬化後にグリップ形状に成形していきます。
ブランクに接着するときにコルクの円筒部分と平面部分との直角度が出ていないとコルクを積層した際に隙間が空いたり、一部が局所的に圧縮されたりしてしまいます。
私は、コルクをブランクに接着する際には、1個ずつ旋盤に取り付けて回転させ、外形と平面部分との直角度を確認しています。
旋盤を回転させコルクの平面部分が振れていなければ直角度は問題ないので、コルクを反転させ、反対面の振れを確認します。問題なければ必要に応じてドリルで穴径を調整し、接着前の下準備は終了です。
旋盤を回転させコルクの平面部分が振れている場合はバイトで振れを取り除き、ペーパーで面を均します。両面とも確認して必要に応じて修正します。
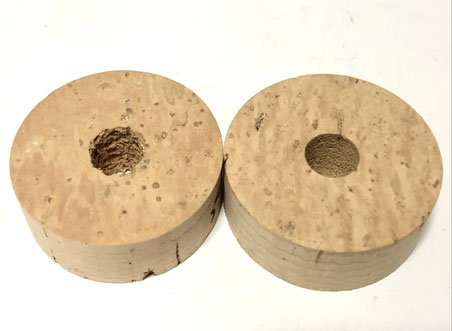
コルクは1個ずつブランクに接着したほうが強度が出ると思っています。
グリップ形状に成形したコルクグリップをブランクに差し込んで接着する方法は、個別接着よりも信頼性が低いと思っています。
さて、穴あきコルクにはφ6mm程度の穴が開いた状態で納入されています。
この穴径のまま使用できるブランクであれば問題ないのですが、たいていの場合穴径を大きくするため、コルクを旋盤にチャックしてドリルで穴径を大きくします。
コルクは木材や金属に比べ加工抵抗が小さいため簡単に穴が開いてしまいます。
けれども、実際はドリルにより切削加工されているのではなく、ドリルの刃によってコルクがむしられていることが多いのです。
写真左はφ6mmの穴の開いたコルクに8mmのドリルで何気なく加工したものです。
写真右は同じくφ6mmの穴の開いたコルクに8mmのドリルでゆっくりと穴を開けたコルクです
左はむしられた状態になっており、右は切削加工された仕上がりになっていることがお判りいただけると思います。
切削抵抗なく簡単に加工できるからと言って雑な加工を行なうとコルクがむしれてしまうので、丁寧に芯押し台を回して切削加工を行なうようにしたいものです。
後は、片方側からドリルを突っ切るのではなく、半分程度片側からドリル加工して、コルクを反転させ、残りを加工するようにしたほうがムシレ等を低減させることができると思います。
簡単な加工ですが、手を抜かず、丁寧に加工すれば綺麗な加工が出来ます。
写真のような違いがあれば、グリップの一番先端側のコルクの状態に影響するので、ワインディングチェックでごまかしたりしなくても、綺麗なコルク端面を露出させることができます。