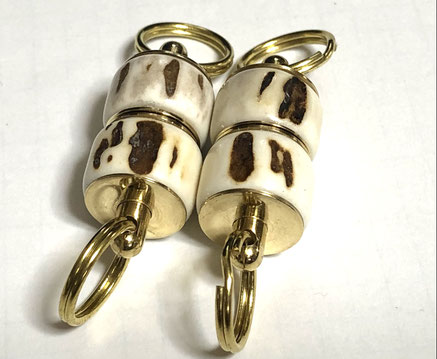
最近は小物の加工が続いております。
小物はイベントが近づいたときに慌てて加工することが多かったのですが、少しづつ時間のある時に加工を行なっています。
まずはMagnet Releaserです。
鹿角タイプのMagnet Releaserですが、外径が合わないと上手く鹿角の模様が出ないので、1本の鹿角から1セットから2セット程度しか加工することが出来ません。
写真の関係かあまり綺麗に見えませんが、実物はもう少し綺麗に輝いております。
~30センチ程度の内径のランディングネット用のMagnet Releaserです。
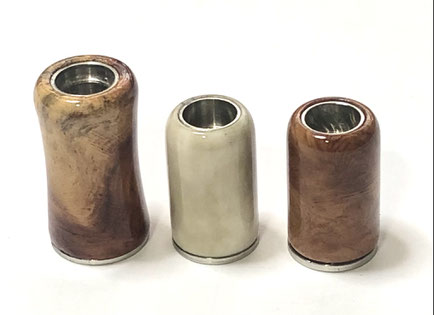
次はノブです。
最近は常にノブの加工のためにリールが送付されている状態で、色んなノブを加工しております。
ノブの形状については、径、長さ、形状の好みは人それぞれなので、出来るだけ要望に即した形状に加工したいと考えております。
写真にあるように、私が加工するノブにはノブの内側に金属パーツがあります。
この金属パーツは「メタルコア」と呼んでおり、このパーツがあることにより、温度変化によってノブが伸縮してもネジと干渉することもないようにネジとメタルコアの熱膨張を出来るだけ合わせ込むことにより、温度変化による影響を排除しております。
また、転倒、リール落下等により、ノブが破損してもメタルコアだけでもリールを回転させることができます。
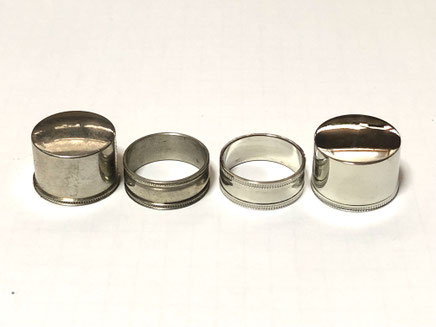
最後はリールシート金具の加工です。
左のCap&Ringと同じサイズの金具を加工して欲しいとの依頼があり、試作的に加工してみました。
加工して分かったことなんですが、サイズをあと0.2mm程度調整することで使用できる原材料サイズを変更することができるので、材料コスト、加工時間削減が出来そうです。
ある程度まとまった数を加工しようと考えた場合の加工方法に関しては、Ringは長めの内径加工をしたものに複数個分のRing加工を行ない、切断して複数個連続加工は出来るのですが、Capに関しては止まり穴加工なので、連続加工が出来ません。
さらにはCapの写真のTop部分にはR加工を行なっているので、突っ切り加工で個別に分離したCapを再度加工する必要があり手間がかかりますが、この加工については効率的な加工方法がありません。
内径加工をNC加工する場合は、その後の突っ切り加工のために突っ切りバイトに付け替えると、突っ切り後に再度内径加工する際にはバイト位置の計測、補正等が必要になるので、1つの加工を大量に行う方式を採用していますが、その際には材料を子切りにしたものを大量に準備する必要があり、そうすると加工残りで使えない部分が結構ストックされ、それは材料効率が悪く、なかなか根深い問題なのです。
研磨にも結構な時間がかる作業ですが丁寧な仕事が求められる作業なので、手を抜かずやりたい仕事です。