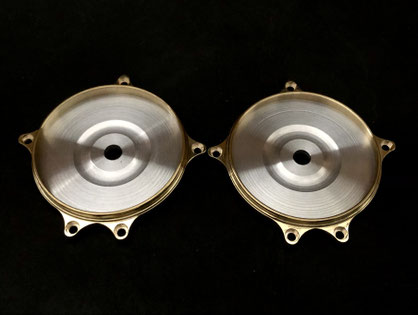
真鍮製のフレームとジュラルミン製のフェイスプレート いわゆるバイメタルと言われるリールを加工しております。
異種金属を貼り合せ、その熱膨張差によって変形させるバイメタルとは少し違って、い異種金属ですが、熱膨張差によって変形してもらっては困るのです。
フェイスプレート径は56mmなので、真鍮とジュラルミンとの熱膨張差3×10-6/kであれば1℃あたり0.17μm、50℃の温度変化で約8.5μmの伸びの差になります。
ではこの伸びの差が影響するのかどうかですが、フレームに対してフェイスプレートを圧入しているわけではなく、少し隙間を設けてその部分を接着しているので、膨張差による影響はありません。
接着剤は完全に硬化するエポキシ等であればこの伸びの差により場合によってはクラックが発生したりする場合があるかもしれませんが、弾性接着剤を使用しているので、この伸びは接着剤の弾性で追従可能で、影響はありません。
話は少しそれましたが、バイメタルリールでも熱膨張を気にすることなく使用していただけます。
フレームは研磨しておりますが、フェイスプレートは窪み加工までは終わっていますが、裏面の加工、外形加工、研磨加工はまだこれからです。
しかしこのh核的大きなパーツが加工できると一気にリールらしくなるので、やれやれなのですが、これからの細かなパーツが案外時間が掛かるのです。
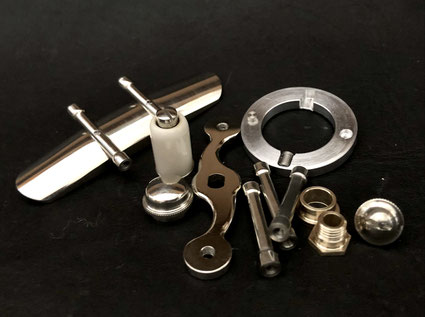
リールフットは前回加工が終わっていましたが、ノブ、S字ハンドル、ピラー、軸受け、飾りネジ、ラチェットパーツ等々の加工を行なっていました。
リールは複数台同時加工をしていますので、実際にはこの数倍のパーツ加工を行なっているのです。
例えばピラーですが、1個のリールに5本のピラーが必要です。
その内の2本はリールフットに装着されます。
このピラーを加工するには、φ5mmもニッケルシルバー棒から約25mmに切り出し、端面を加工して長さを揃えます。
両端にセンター穴を開け、φ2.1mmのドリル加工を行ない、M2.6mmのタップ加工を行ないます。
外形加工を行ない、フットのピラーには中心にM2のネジ穴を加工します。
全体を研磨して完了です。
仮に3台のリールを加工している場合は15本のピラーを作製することになります。
丸1日はたらいてピラー15本しか加工できない日もあるのです。
それだけ時間の掛かる仕事なのです。研磨をしなければもっと加工は出来ますが、研磨してなんぼの世界でリールを作製している私にとっては、機械加工のままはあり得ないのです。
それ以外にもS字ハンドル、ノブ、飾りネジ等の研磨があります
「見えるところの手を抜く奴は見えないところでも手を抜く」当たり前のことです。
ですから、「神は細部に宿る」
この思いで今日も爪の中まで真っ黒にしながらパーツを磨いています。
綺麗なリールが好きなもので.....。